Lean Six Sigma Case study in Chennai
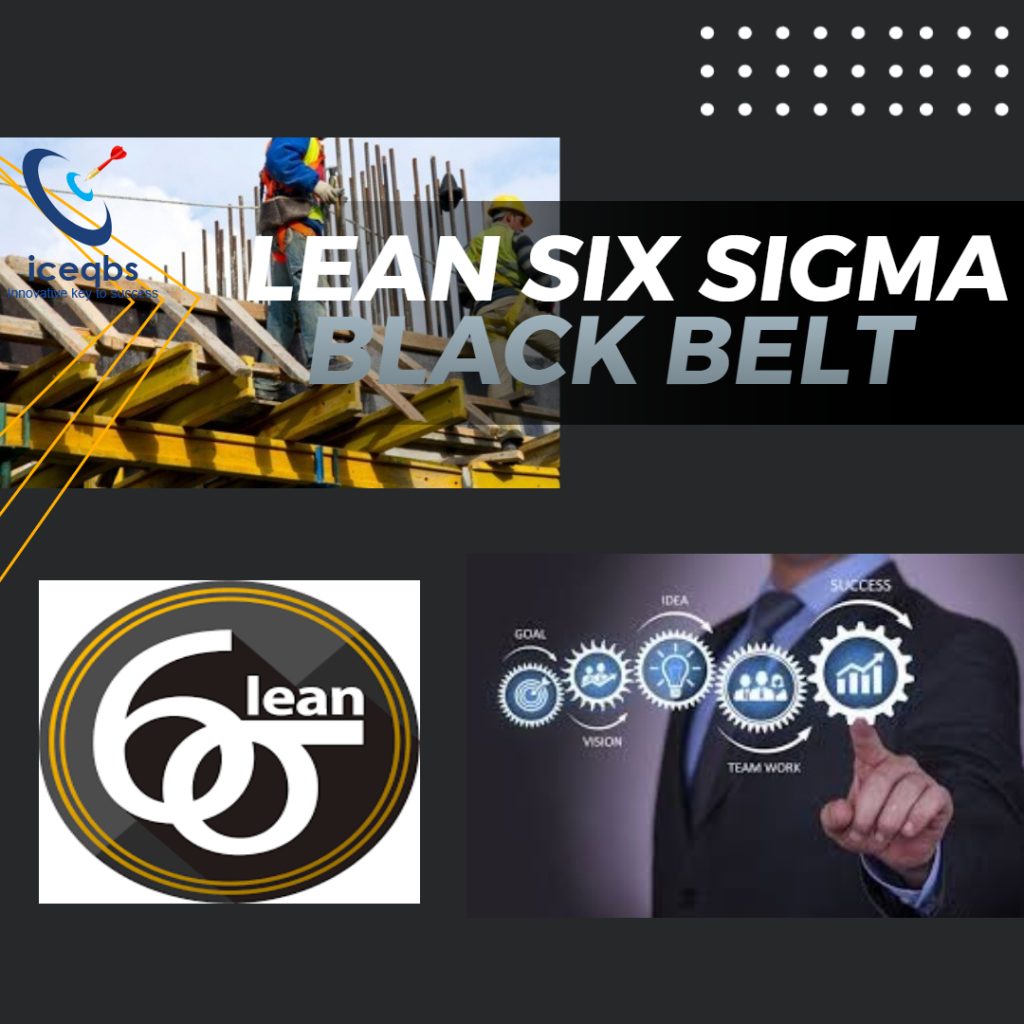
Lean Six Sigma Case study in Chennai In today’s competitive business environment, organizations constantly seek ways to enhance operational efficiency and streamline processes to deliver better products and services to customers. Lean Six Sigma methodologies offer a systematic approach to identify and eliminate waste while reducing variability in processes. This case study illustrates how a manufacturing company successfully applied Lean Six Sigma principles to optimize its production processes and achieve significant improvements in operational efficiency.
Background: XYZ Manufacturing, a leading player in the automotive parts industry, faced challenges in meeting customer demands due to inefficiencies in its production processes. The company experienced delays, defects, and high operational costs, impacting its competitiveness and customer satisfaction levels. To address these issues, XYZ Manufacturing decided to implement Lean Six Sigma methodologies to identify root causes of problems and implement sustainable solutions.
Methodology: The Lean Six Sigma team at XYZ Manufacturing began by conducting a thorough analysis of the current production processes, mapping out each step from raw material procurement to final product delivery. They identified various sources of waste, including overproduction, unnecessary inventory, defects, and waiting times. Using tools such as value stream mapping and process flow analysis, the team pinpointed areas for improvement and set specific goals for reducing waste and improving process efficiency.
Implementation: With a clear understanding of the challenges and opportunities, the Lean Six Sigma team initiated targeted improvement projects. They implemented visual management systems to enhance transparency and communication on the shop floor, enabling workers to identify and address issues promptly. Additionally, they introduced standardized work procedures and trained employees on Lean Six Sigma principles to foster a culture of continuous improvement.
One of the key initiatives was the implementation of a kanban system to regulate the flow of materials and prevent overproduction. By establishing pull-based replenishment mechanisms, XYZ Manufacturing reduced inventory levels and minimized stockouts, leading to smoother production operations and reduced lead times.
Another focus area was reducing defects and rework. The team conducted root cause analysis using tools such as fishbone diagrams and Pareto charts to identify the underlying causes of defects. They then implemented corrective actions, such as improving equipment maintenance procedures and providing additional training to operators, resulting in a significant decrease in defect rates and rework costs.
Results: The implementation of Lean Six Sigma methodologies yielded impressive results for XYZ Manufacturing. The company achieved a 30% reduction in lead times, allowing it to respond more quickly to customer demands and improve overall responsiveness. Additionally, defect rates decreased by 50%, resulting in substantial cost savings and enhanced product quality. By optimizing its production processes, XYZ Manufacturing improved operational efficiency and gained a competitive edge in the market.
Conclusion: This case study highlights the transformative impact of Lean Six Sigma methodologies on operational efficiency within XYZ Manufacturing. By systematically identifying and eliminating waste, the company was able to streamline its processes, reduce costs, and enhance customer satisfaction. The success of this initiative underscores the importance of continuous improvement and a data-driven approach to achieving operational excellence in today’s dynamic business environment.